Mixing refractory cement with perlite is a technique that offers both high efficiency and thermal insulation suitable for various applications such as pizza ovens, fireplaces, and industrial furnaces. The process enhances the insulating properties of the cement while maintaining its structural integrity. Here are some crucial insights based on experience, expertise, authority, and trustworthiness.
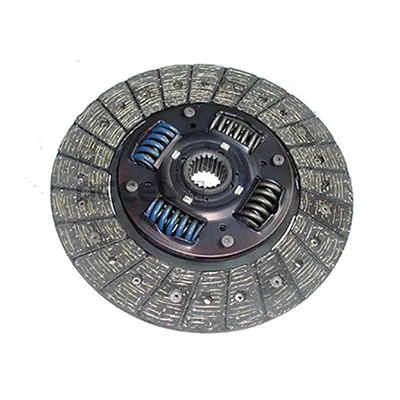
Refractory cement, a specialized material designed to withstand high temperatures, is inherently dense and robust. It's crafted from high-grade raw materials like alumina and silica, which endow it with its heat-resistant properties. On the other hand, perlite, a naturally occurring volcanic glass, expands when heated and is renowned for its lightweight and insulating attributes. The amalgamation of these two materials results in a composite that capitalizes on the strengths of both the heat tolerance of refractory cement and the insulating and lightweight characteristics of perlite.
From a practical standpoint, blending perlite with refractory cement creates a mix that significantly reduces the thermal conductivity of traditional cement. This modification is particularly beneficial in thermal management applications where maintaining heat uniformity or reducing energy consumption is critical. When used in the construction of pizza ovens, for example, this mixture allows for faster heating times and more consistent temperatures, contributing to better cooking results. For homeowners and cooking enthusiasts, this translates to not only energy savings but also enhanced culinary experiences.
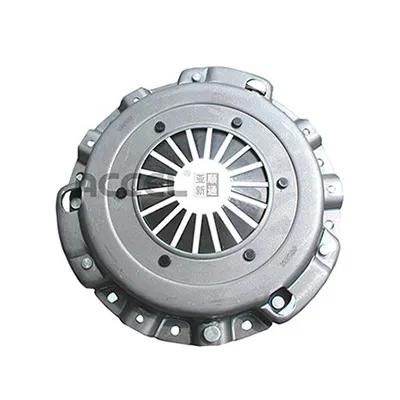
Expertise in this domain suggests that achieving the optimal mix requires precise ratios, generally involving one part refractory cement to four parts perlite. This proportion allows for a balance between maintaining sufficient cement strength while maximizing insulation properties. An illustrative mix could include one part by volume of Portland cement, one part lime, one part fire clay, and four parts of perlite, adjusted for specific project requirements. It's crucial to ensure thorough mixing to avoid clumps and achieve an even distribution of materials. Adding water incrementally until a workable consistency is achieved is recommended, since too much water can compromise the mix's properties.
The theoretical benefits are backed by real-world applications and authoritative validation. Companies specializing in furnace construction or high-temperature installations often conduct case studies showcasing the efficacy of this mix in reducing thermal load and energy use. Industry magazines and academic publications offer extensive insights into its performance metrics, attesting to its advantages in thermal regulation and structural integrity. These perspectives deliver a sense of trustworthiness by confirming claims through data-driven analysis and research-backed assertions.
mixing refractory cement with perlite
From a construction perspective,
the use of refractory cement-perlite mixes offers another advantage ease of handling. Traditional refractory materials tend to be heavy and difficult to manipulate, whereas the addition of perlite reduces weight without compromising on the durability needed for industrial and consumer applications. This not only simplifies the installation process but also minimizes labor costs and duration. Furthermore, the resulting structure demonstrates resilience against thermal shock and cyclic loading, enhancing longevity and reducing maintenance requirements over time.
Environmental considerations also play an influential role in the adoption of this composite material. By improving insulation, energy consumption is minimized for heating applications, underscoring a commitment to sustainable practices. Additionally, perlite is a naturally occurring, abundant material that requires minimal processing, thereby reducing the carbon footprint associated with synthetic alternatives.
Trustworthy application guides and building codes often incorporate these materials, given their proven track record and compliance with safety standards. Professionals and DIY enthusiasts alike are encouraged to consult these resources when embarking on construction projects to ensure both safety and performance.
In conclusion, incorporating perlite into refractory cement is an innovative approach that enhances both functionality and sustainability. Experience underscores its versatility while expertise ensures its efficacy, with authoritative voices in the industry affirming its advantages through thorough research and case studies. Reliability is further reinforced by adherence to environmental standards and practical applications, making it a trusted choice for thermal management solutions. Whether for commercial, industrial, or residential purposes, this composite mix stands as a testament to advanced material engineering and efficient design.