Refractory cenospheres have emerged as a game-changer in the materials industry, revolutionizing the way companies approach high-temperature applications. Known for their lightweight nature and superior thermal resistance, these hollow, spherical particles are derived from the byproducts of coal combustion. They are increasingly gaining traction across various sectors, particularly in refractory and insulation applications.
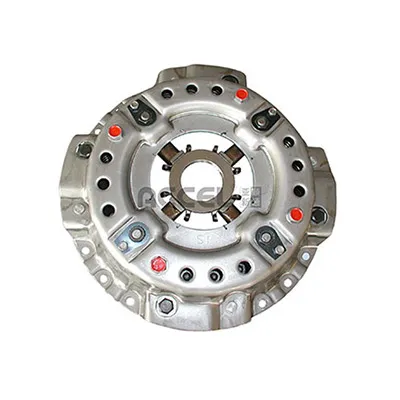
The remarkable lightweight structure of refractory cenospheres, typically comprising silica and alumina, contributes significantly to reducing the weight of composite materials without compromising strength and integrity. This attribute is particularly beneficial in applications demanding both durability and weight reduction, such as aerospace and automotive manufacturing. Engineers and material scientists consistently report improved fuel efficiency and load management in vehicles and aircraft that utilize components reinforced with cenospheres.
Experts in material engineering appreciate the unique combination of properties offered by these tiny spheres. Apart from being lightweight, their high melting point, often exceeding 1200°C, makes them ideal for extreme temperature environments. This characteristic is critical in industries such as metallurgy, where materials are frequently subjected to intense heat. Refractory cenospheres provide a stable, efficient barrier against thermal loss, which enhances energy conservation and optimizes performance. This energy efficiency translates to significant cost savings, a benefit highly valued by industrial operations managers focused on optimizing output while minimizing expenses.
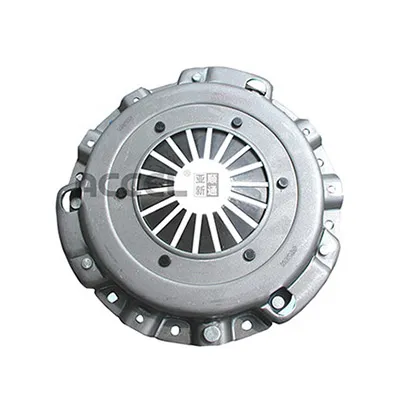
The use of refractory cenospheres extends beyond thermal applications. Their nonporous nature ensures minimal moisture absorption, which in turn leads to greater resistance to chemical attack. This offers a substantial advantage in chemical processing industries where materials are exposed to corrosive substances. The reduced permeability ensures a longer lifespan of equipment and infrastructure, reducing maintenance costs and downtime, thus maintaining seamless operational efficiency.
refractory cenospheres
The adaptability of refractory cenospheres in creating high-performance, lightweight composites has made them a material of choice for manufacturers seeking to innovate and improve product offerings. In construction, these cenospheres contribute to lighter yet stronger concrete formulations, leading to structures that are not only robust but also easier and more cost-effective to transport and assemble. Architects and builders report considerable improvements in project timelines and structural integrity when utilizing cenosphere-enhanced materials.
From a sustainability perspective, the use of cenospheres is notable for its role in recycling industrial byproducts, thereby reducing environmental waste. Companies embracing this shift not only leverage the technical benefits but also enhance their corporate responsibility credentials, appealing to environmentally conscious stakeholders. Material suppliers specializing in refractory cenospheres are increasingly seen as authoritative voices in promoting sustainable industry practices.
Trust in the consistent quality and performance of refractory cenosphere products is further reinforced by rigorous testing and quality assurance processes. Manufacturers often adhere to stringent industry standards and certifications to ensure that the material characteristics meet or exceed client specifications. This quality assurance builds trust among buyers and stakeholders who demand reliability and performance in high-stakes applications.
In conclusion, the incorporation of refractory cenospheres into high-temperature applications presents a fusion of technical excellence and cost-efficiency. Their unique properties not only enhance the functionality and performance of materials across various industries but also align with a growing emphasis on sustainability and environmental stewardship. As their application expands, the expertise surrounding their utilization positions them as an authoritative solution in addressing contemporary engineering and environmental challenges. Companies investing in this innovative material are poised to lead in performance, efficiency, and responsible resource management.