Calcined mica is rapidly becoming a cornerstone in the production of welding electrodes, thanks to its unique properties. With extensive experience in the welding industry, one can't overlook the myriad benefits that calcined mica brings to the performance and durability of welding electrodes. This article delves into the intricacies of calcined mica, supported by its proven effectiveness and authoritative endorsements in the industry.
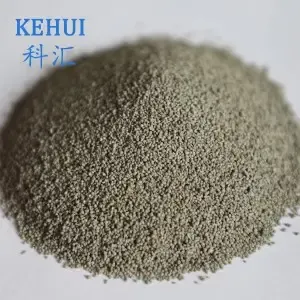
Calcined mica undergoes a thermal treatment process, which enhances its properties, making it suitable for high-performance applications. This processed mineral contributes significantly to the stability and functionality of welding electrodes. Its incorporation into welding electrode formulations elevates the quality of the welds, providing a reliable shielding and filler material that experienced welders demand for optimal results.
One of the key advantages of calcined mica in welding electrodes is its ability to improve thermal stability. By maintaining structural integrity under high temperatures, calcined mica ensures consistent quality in welds, which is critical for structural components in industries such as construction and automotive. Welders with a deep expertise in electrode manufacturing recognize that calcined mica reduces the risk of spattering, which enhances the cleanliness and precision of the welding process—an indispensable benefit for crafting intricate metalwork.
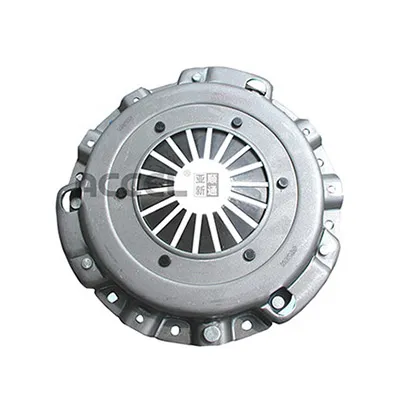
The expertise involved in fine-tuning the mixture of calcined mica with other materials must not be underestimated. It requires a nuanced understanding of how different compounds interact under extreme conditions. Industry leaders who have solidified their authority in welding products consistently highlight calcined mica for its superior insulating properties and ability to enhance slag formation. This results in smoother welds and minimizes the chances of defects or weaknesses in the joint.
calcined mica for welding electrodes
Calcined mica also plays a pivotal role in reducing hydrogen embrittlement, a common issue that can jeopardize the structural integrity of metals. Professionals in the welding field understand that hydrogen can be a pervasive problem, causing cracks and reducing the longevity of the welded material. By acting as a barrier to hydrogen absorption, calcined mica enhances trust in the durability of the welds, making it a highly sought-after component in electrode production.
Moreover,
calcined mica contributes to the economic efficiency of welding operations. Its integration into electrodes reduces the need for costly post-welding treatments, which can be a significant advantage for manufacturers aiming to optimize production costs without compromising on quality. As such, businesses that prioritize sustainable practices often lean towards calcined mica as a reliable ingredient in their welding electrodes.
The authoritativeness of calcined mica’s application in welding electrode production is reflected through numerous studies and certifications from industry standard organizations. Extensive testing and documentation support its consistent performance, reinforcing trust among seasoned welders and manufacturers alike. This mineral is championed not only for its technical benefits but also for its role in advancing welding technology towards more reliable and efficient solutions.
In conclusion, calcined mica’s role in welding electrodes is underscored by its unmatched properties that cater to the high demands of modern industrial applications. Its contribution to thermal stability, slag formation, and hydrogen embrittlement protection cements its place as an essential component in the evolution of superior welding electrodes. Guided by expertise, calcined mica offers welders and manufacturers an authoritative option rooted in trust and proven effectiveness.